Tehnologija rezanja pločica, kao ključni korak u procesu proizvodnje poluvodiča, izravno je povezana s performansama čipa, prinosom i troškovima proizvodnje.
#01 Pozadina i značaj rezanja oblatne
1.1 Definicija rezanja oblatne
Rezanje pločica (također poznato kao scribing) je bitan korak u proizvodnji poluvodiča, usmjeren na dijeljenje obrađenih pločica u više pojedinačnih čipova. Ovi čipovi obično sadrže potpunu funkcionalnost sklopa i ključne su komponente koje se u konačnici koriste u proizvodnji elektroničkih uređaja. Kako dizajn čipova postaje sve složeniji, a dimenzije se nastavljaju smanjivati, zahtjevi za preciznošću i učinkovitošću tehnologije rezanja pločica postaju sve stroži.
U praktičnim operacijama, rezanje pločica obično koristi visokoprecizne alate poput dijamantnih oštrica kako bi se osiguralo da svaki kalup ostane neoštećen i potpuno funkcionalan. Ključni koraci uključuju pripremu prije rezanja, preciznu kontrolu tijekom procesa rezanja i kontrolu kvalitete nakon rezanja.
Prije rezanja, pločica mora biti označena i pozicionirana kako bi se osigurale točne putanje rezanja. Tijekom rezanja, parametri poput pritiska alata i brzine moraju se strogo kontrolirati kako bi se spriječilo oštećenje pločice. Nakon rezanja provode se sveobuhvatne kontrole kvalitete kako bi se osiguralo da svaki čip zadovoljava standarde performansi.
Temeljna načela tehnologije rezanja pločica obuhvaćaju ne samo odabir opreme za rezanje i postavljanje procesnih parametara, već i utjecaj mehaničkih svojstava i karakteristika materijala na kvalitetu rezanja. Na primjer, silicijeve pločice s niskim dielektričnim faktorom (low-k), zbog svojih lošijih mehaničkih svojstava, vrlo su osjetljive na koncentraciju naprezanja tijekom rezanja, što dovodi do kvarova poput ljuštenja i pucanja. Niska tvrdoća i krhkost materijala s niskim dielektričnim faktorom čine ih sklonijima strukturnim oštećenjima pod mehaničkom silom ili toplinskim naprezanjem, posebno tijekom rezanja. Kontakt između alata i površine pločice, zajedno s visokim temperaturama, može dodatno pogoršati koncentraciju naprezanja.
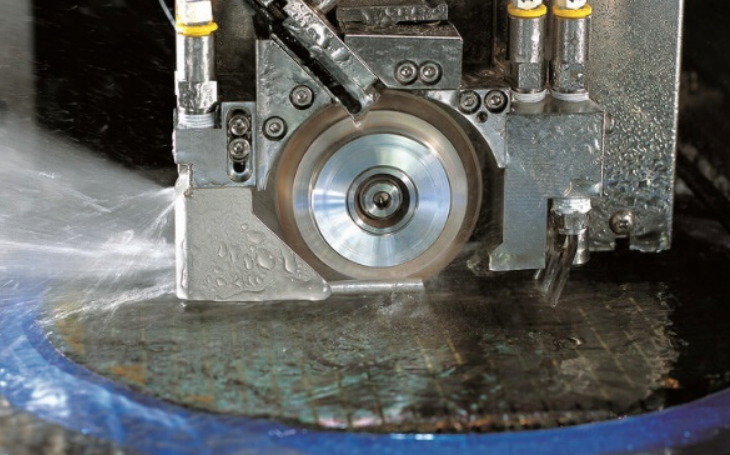
S napretkom u znanosti o materijalima, tehnologija rezanja pločica proširila se izvan tradicionalnih poluvodiča na bazi silicija i uključila nove materijale poput galijevog nitrida (GaN). Ovi novi materijali, zbog svoje tvrdoće i strukturnih svojstava, predstavljaju nove izazove za procese rezanja, zahtijevajući daljnja poboljšanja alata i tehnika rezanja.
Kao ključni proces u poluvodičkoj industriji, izrada pločica se i dalje optimizira kao odgovor na rastuće zahtjeve i tehnološki napredak, postavljajući temelje za buduću mikroelektroniku i tehnologije integriranih krugova.
Poboljšanja u tehnologiji rezanja pločica nadilaze razvoj pomoćnih materijala i alata. Ona također obuhvaćaju optimizaciju procesa, poboljšanja performansi opreme i preciznu kontrolu parametara rezanja. Cilj ovih napredaka je osigurati visoku preciznost, učinkovitost i stabilnost u procesu rezanja pločica, zadovoljavajući potrebe poluvodičke industrije za manjim dimenzijama, većom integracijom i složenijim strukturama čipova.
područje poboljšanja | Specifične mjere | Efekti |
Optimizacija procesa | - Poboljšati početne pripreme, kao što su preciznije pozicioniranje pločice i planiranje putanje. | - Smanjite pogreške rezanja i poboljšajte stabilnost. |
- Minimizirajte pogreške rezanja i poboljšajte stabilnost. | - Usvojite mehanizme praćenja i povratne informacije u stvarnom vremenu za podešavanje tlaka, brzine i temperature alata. | |
- Smanjuje stopu loma pločice i poboljšava kvalitetu čipa. | ||
Poboljšanje performansi opreme | - Koristiti visokoprecizne mehaničke sustave i naprednu tehnologiju automatizacije upravljanja. | - Poboljšajte točnost rezanja i smanjite otpad materijala. |
- Uvesti tehnologiju laserskog rezanja pogodnu za pločice od materijala visoke tvrdoće. | - Poboljšati učinkovitost proizvodnje i smanjiti ručne pogreške. | |
- Povećati automatizaciju opreme za automatsko praćenje i podešavanje. | ||
Precizna kontrola parametara | - Fino podešavanje parametara poput dubine rezanja, brzine, vrste alata i metoda hlađenja. | - Osigurati integritet čipa i električne performanse. |
- Prilagodite parametre na temelju materijala, debljine i strukture pločice. | - Povećati prinos, smanjiti otpad materijala i sniziti troškove proizvodnje. | |
Strateški značaj | - Kontinuirano istraživati nove tehnološke putove, optimizirati procese i poboljšavati mogućnosti opreme kako bi se zadovoljile potrebe tržišta. | - Poboljšati prinos i performanse proizvodnje čipova, podržavajući razvoj novih materijala i naprednih dizajna čipova. |
1.2 Važnost rezanja oblatne na kockice
Rezanje pločica igra ključnu ulogu u procesu proizvodnje poluvodiča, izravno utječući na sljedeće korake, kao i na kvalitetu i performanse konačnog proizvoda. Njegova važnost može se detaljno opisati na sljedeći način:
Prvo, točnost i dosljednost rezanja ključne su za osiguranje prinosa i pouzdanosti čipa. Tijekom proizvodnje, pločice prolaze kroz više koraka obrade kako bi se formirale brojne složene strukture krugova, koje se moraju precizno podijeliti na pojedinačne čipove (matrice). Ako postoje značajne pogreške u poravnanju ili rezanju tijekom procesa rezanja, krugovi se mogu oštetiti, što utječe na funkcionalnost i pouzdanost čipa. Stoga, visokoprecizna tehnologija rezanja ne samo da osigurava integritet svakog čipa, već i sprječava oštećenje unutarnjih krugova, poboljšavajući ukupnu stopu prinosa.
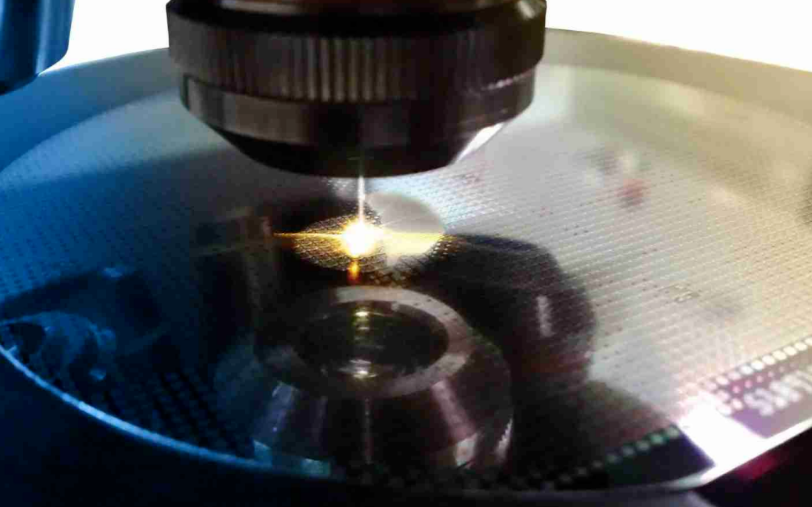
Drugo, rezanje pločica ima značajan utjecaj na učinkovitost proizvodnje i kontrolu troškova. Kao ključni korak u proizvodnom procesu, njegova učinkovitost izravno utječe na napredak sljedećih koraka. Optimizacijom procesa rezanja, povećanjem razine automatizacije i poboljšanjem brzine rezanja, ukupna učinkovitost proizvodnje može se uvelike poboljšati.
S druge strane, rasipanje materijala tijekom rezanja ključni je faktor u upravljanju troškovima. Korištenje naprednih tehnologija rezanja ne samo da smanjuje nepotrebne gubitke materijala tijekom procesa rezanja, već i povećava iskorištenost pločice, čime se smanjuju troškovi proizvodnje.
S napretkom u tehnologiji poluvodiča, promjeri pločica nastavljaju se povećavati, a gustoća sklopova raste sukladno tome, što postavlja veće zahtjeve na tehnologiju rezanja. Veće pločice zahtijevaju precizniju kontrolu putanja rezanja, posebno u područjima sklopova visoke gustoće, gdje čak i mala odstupanja mogu uzrokovati neispravnost više čipova. Osim toga, veće pločice uključuju više linija rezanja i složenije korake procesa, što zahtijeva daljnja poboljšanja preciznosti, dosljednosti i učinkovitosti tehnologija rezanja kako bi se odgovorilo na te izazove.
1.3 Postupak rezanja oblatne
Proces rezanja vafla obuhvaća sve korake od faze pripreme do konačne kontrole kvalitete, pri čemu je svaka faza ključna za osiguranje kvalitete i performansi narezanih čipsa. U nastavku slijedi detaljno objašnjenje svake faze.
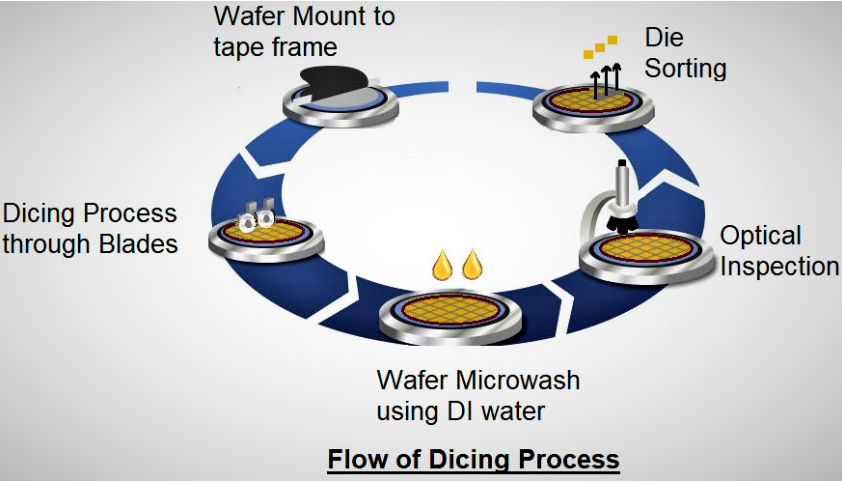
Faza | Detaljan opis |
Pripremna faza | -Čišćenje oblatneKoristite vodu visoke čistoće i specijalizirana sredstva za čišćenje, u kombinaciji s ultrazvučnim ili mehaničkim ribanjem, za uklanjanje nečistoća, čestica i onečišćujućih tvari, osiguravajući čistu površinu. -Precizno pozicioniranjeKoristite visokopreciznu opremu kako biste osigurali da je pločica precizno podijeljena duž dizajniranih putanja rezanja. -Fiksiranje pločicaPričvrstite pločicu na okvir trake kako biste održali stabilnost tijekom rezanja i spriječili oštećenja od vibracija ili pomicanja. |
Faza rezanja | -Rezanje oštricomZa fizičko rezanje koristite brze rotirajuće oštrice s dijamantnim premazom, prikladne za materijale na bazi silicija i isplative. -Lasersko rezanje kockicaKoristite visokoenergetske laserske zrake za beskontaktno rezanje, idealno za krhke ili visokotvrde materijale poput galijevog nitrida, nudeći veću preciznost i manji gubitak materijala. -Nove tehnologijeUvesti tehnologije laserskog i plazma rezanja kako bi se dodatno poboljšala učinkovitost i preciznost uz istovremeno smanjenje zona utjecaja topline. |
Faza čišćenja | - Koristite deioniziranu vodu (DI vodu) i specijalizirana sredstva za čišćenje, u kombinaciji s ultrazvučnim ili raspršivačkim čišćenjem, za uklanjanje ostataka i prašine nastale tijekom rezanja, sprječavajući da ostaci utječu na kasnije procese ili električne performanse strugotine. - Visokočista deionizirana voda sprječava unošenje novih onečišćujućih tvari, osiguravajući čisto okruženje za pločice. |
Faza inspekcije | -Optički pregledKoristite optičke sustave za detekciju u kombinaciji s AI algoritmima za brzo prepoznavanje nedostataka, osiguravajući da nema pukotina ili oštećenja na kockicama, poboljšavajući učinkovitost inspekcije i smanjujući ljudske pogreške. -Mjerenje dimenzijaProvjerite odgovaraju li dimenzije čipa specifikacijama dizajna. -Ispitivanje električnih performansiOsigurati da električne performanse kritičnih čipova zadovoljavaju standarde, jamčeći pouzdanost u kasnijim primjenama. |
Faza sortiranja | - Koristite robotske ruke ili vakuumske usisne čašice za odvajanje kvalificiranih čipova od okvira trake i automatsko sortiranje na temelju performansi, osiguravajući učinkovitost i fleksibilnost proizvodnje uz istovremeno poboljšanje preciznosti. |
Proces rezanja pločica uključuje čišćenje, pozicioniranje, rezanje, čišćenje, inspekciju i sortiranje pločica, pri čemu je svaki korak ključan. S napretkom u automatizaciji, laserskom rezanju i tehnologijama inspekcije umjetnom inteligencijom, moderni sustavi za rezanje pločica mogu postići veću preciznost, brzinu i manji gubitak materijala. U budućnosti će nove tehnologije rezanja poput lasera i plazme postupno zamijeniti tradicionalno rezanje oštricama kako bi se zadovoljile potrebe sve složenijih dizajna čipova, dodatno potičući razvoj procesa proizvodnje poluvodiča.
Tehnologija rezanja pločica i njezini principi
Slika prikazuje tri uobičajene tehnologije rezanja pločica:Rezanje oštricom,Lasersko rezanje kockicaiPlazma kockiceU nastavku slijedi detaljna analiza i dodatno objašnjenje ove tri tehnike:
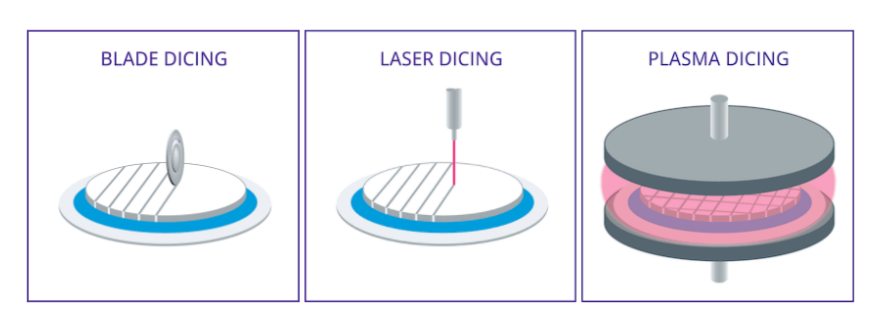
U proizvodnji poluvodiča, rezanje pločica ključan je korak koji zahtijeva odabir odgovarajuće metode rezanja na temelju debljine pločice. Prvi korak je određivanje debljine pločice. Ako debljina pločice prelazi 100 mikrona, kao metoda rezanja može se odabrati rezanje oštricom. Ako rezanje oštricom nije prikladno, može se koristiti metoda rezanja lomljenjem, koja uključuje tehnike rezanja s gravurom i rezanja oštricom.
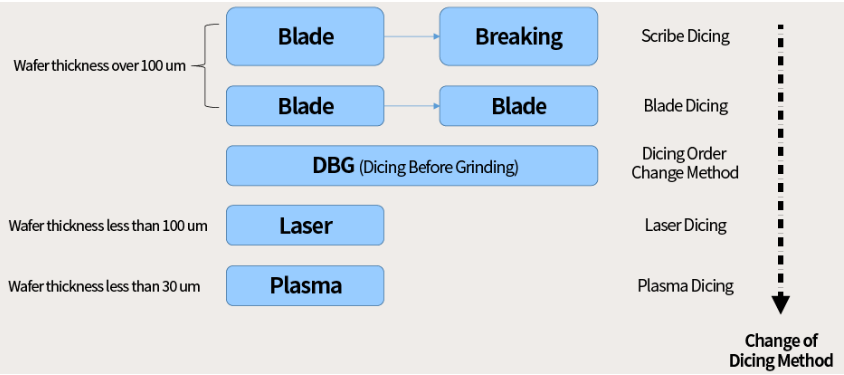
Kada je debljina pločice između 30 i 100 mikrona, preporučuje se DBG (Dice Before Grinding - rezanje prije mljevenja). U tom slučaju, za postizanje najboljih rezultata može se odabrati rezanje s ocrtavanjem, rezanje s oštricom ili prilagođavanje redoslijeda rezanja prema potrebi.
Za ultra tanke pločice debljine manje od 30 mikrona, lasersko rezanje postaje preferirana metoda zbog svoje sposobnosti preciznog rezanja tankih pločica bez nanošenja prekomjernih oštećenja. Ako lasersko rezanje ne može zadovoljiti specifične zahtjeve, plazma rezanje može se koristiti kao alternativa. Ovaj dijagram toka pruža jasan put donošenja odluka kako bi se osiguralo da se odabere najprikladnija tehnologija rezanja pločica pod različitim uvjetima debljine.
2.1 Tehnologija mehaničkog rezanja
Tehnologija mehaničkog rezanja tradicionalna je metoda rezanja pločica. Osnovni princip je korištenje dijamantnog brusnog kotača velike brzine kao alata za rezanje pločice. Ključna oprema uključuje vreteno s zračnim ležajem koje pokreće dijamantni brusni kotač velikim brzinama kako bi se precizno rezalo ili žljebilo duž unaprijed definirane putanje rezanja. Ova se tehnologija široko koristi u industriji zbog niske cijene, visoke učinkovitosti i široke primjenjivosti.
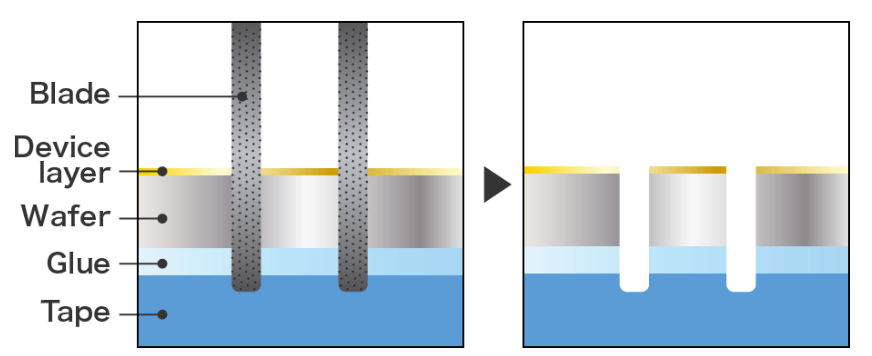
Prednosti
Visoka tvrdoća i otpornost na habanje dijamantnih brusnih alata omogućuje mehaničkoj tehnologiji rezanja prilagodbu potrebama rezanja različitih materijala pločica, bilo da se radi o tradicionalnim materijalima na bazi silicija ili novijim složenim poluvodičima. Njegov rad je jednostavan, s relativno niskim tehničkim zahtjevima, što dodatno potiče njegovu popularnost u masovnoj proizvodnji. Osim toga, u usporedbi s drugim metodama rezanja poput laserskog rezanja, mehaničko rezanje ima kontroliranije troškove, što ga čini prikladnim za potrebe proizvodnje velikih količina.
Ograničenja
Unatoč brojnim prednostima, tehnologija mehaničkog rezanja ima i ograničenja. Prvo, zbog fizičkog kontakta između alata i pločice, preciznost rezanja je relativno ograničena, što često dovodi do dimenzijskih odstupanja koja mogu utjecati na točnost naknadnog pakiranja i testiranja čipa. Drugo, defekti poput odlomljivanja i pukotina mogu se lako pojaviti tijekom procesa mehaničkog rezanja, što ne samo da utječe na stopu prinosa, već može negativno utjecati i na pouzdanost i vijek trajanja čipova. Oštećenja uzrokovana mehaničkim naprezanjem posebno su štetna za proizvodnju čipova visoke gustoće, posebno pri rezanju krhkih materijala, gdje su ti problemi izraženiji.
Tehnološka poboljšanja
Kako bi prevladali ta ograničenja, istraživači kontinuirano optimiziraju mehanički proces rezanja. Ključna poboljšanja uključuju poboljšanje dizajna i odabira materijala brusnih kotača kako bi se poboljšala preciznost i trajnost rezanja. Osim toga, optimizacija strukturnog dizajna i sustava upravljanja opremom za rezanje dodatno je poboljšala stabilnost i automatizaciju procesa rezanja. Ovi napredci smanjuju pogreške uzrokovane ljudskim radnjama i poboljšavaju konzistentnost rezova. Uvođenje naprednih tehnologija inspekcije i kontrole kvalitete za praćenje anomalija u stvarnom vremenu tijekom procesa rezanja također je značajno poboljšalo pouzdanost i prinos rezanja.
Budući razvoj i nove tehnologije
Iako tehnologija mehaničkog rezanja još uvijek zauzima značajno mjesto u rezanju pločica, nove tehnologije rezanja brzo napreduju kako se procesi proizvodnje poluvodiča razvijaju. Na primjer, primjena tehnologije termičkog laserskog rezanja pruža nova rješenja za probleme preciznosti i nedostataka u mehaničkom rezanju. Ova beskontaktna metoda rezanja smanjuje fizičko naprezanje pločice, značajno smanjujući učestalost pucanja i kidanja, posebno pri rezanju krhkijih materijala. U budućnosti će integracija tehnologije mehaničkog rezanja s novim tehnikama rezanja pružiti proizvodnji poluvodiča više mogućnosti i fleksibilnosti, dodatno povećavajući učinkovitost proizvodnje i kvalitetu čipa.
Zaključno, iako tehnologija mehaničkog rezanja ima određene nedostatke, kontinuirana tehnološka poboljšanja i njezina integracija s novim tehnikama rezanja omogućuju joj da i dalje igra važnu ulogu u proizvodnji poluvodiča i održi svoju konkurentnost u budućim procesima.
2.2 Tehnologija laserskog rezanja
Tehnologija laserskog rezanja, kao nova metoda rezanja pločica, postupno je stekla široku pozornost u poluvodičkoj industriji zbog svoje visoke preciznosti, nedostatka mehaničkih oštećenja kontakta i brzih mogućnosti rezanja. Ova tehnologija koristi visoku gustoću energije i sposobnost fokusiranja laserske zrake za stvaranje male zone utjecaja topline na površini materijala pločice. Kada se laserska zraka primijeni na pločicu, generirano toplinsko naprezanje uzrokuje lom materijala na određenom mjestu, postižući precizno rezanje.
Prednosti tehnologije laserskog rezanja
• Visoka preciznostPrecizna sposobnost pozicioniranja laserske zrake omogućuje preciznost rezanja na razini mikrona ili čak nanometara, zadovoljavajući zahtjeve moderne proizvodnje visokopreciznih integriranih krugova visoke gustoće.
• Nema mehaničkog kontaktaLasersko rezanje izbjegava fizički kontakt s pločicom, sprječavajući uobičajene probleme kod mehaničkog rezanja, poput ljuštenja i pucanja, značajno poboljšavajući prinos i pouzdanost čipova.
• Velika brzina rezanjaVelika brzina laserskog rezanja doprinosi povećanoj učinkovitosti proizvodnje, što ga čini posebno prikladnim za scenarije velike brzine i proizvodnje velikih razmjera.
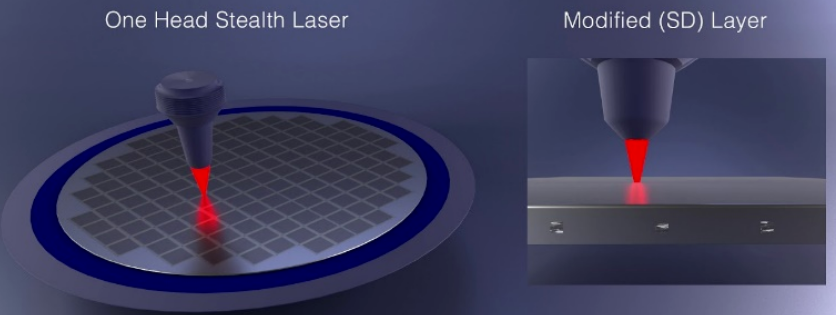
Izazovi s kojima se suočavamo
• Visoki troškovi opremePočetna investicija za opremu za lasersko rezanje je visoka, što predstavlja ekonomski pritisak, posebno za mala i srednja proizvodna poduzeća.
• Složena kontrola procesaLasersko rezanje zahtijeva preciznu kontrolu nekoliko parametara, uključujući gustoću energije, položaj fokusa i brzinu rezanja, što proces čini složenim.
• Problemi u zoni pogođenoj toplinomIako beskontaktna priroda laserskog rezanja smanjuje mehanička oštećenja, toplinsko naprezanje uzrokovano zonom utjecaja topline (HAZ) može negativno utjecati na svojstva materijala pločice. Potrebna je daljnja optimizacija procesa kako bi se taj učinak sveo na minimum.
Smjerovi tehnološkog poboljšanja
Kako bi se riješili ovi izazovi, istraživači se usredotočuju na smanjenje troškova opreme, poboljšanje učinkovitosti rezanja i optimizaciju tijeka procesa.
• Učinkoviti laseri i optički sustaviRazvojem učinkovitijih lasera i naprednih optičkih sustava moguće je smanjiti troškove opreme uz istovremeno povećanje preciznosti i brzine rezanja.
• Optimizacija parametara procesaProvode se dubinska istraživanja interakcije između lasera i materijala pločica kako bi se poboljšali procesi koji smanjuju zonu utjecaja topline, čime se poboljšava kvaliteta rezanja.
• Inteligentni upravljački sustaviRazvoj inteligentnih tehnologija upravljanja ima za cilj automatizirati i optimizirati proces laserskog rezanja, poboljšavajući njegovu stabilnost i konzistentnost.
Tehnologija laserskog rezanja posebno je učinkovita u ultra tankim pločicama i scenarijima visokopreciznog rezanja. Kako se veličine pločica povećavaju, a gustoća sklopova raste, tradicionalne metode mehaničkog rezanja teško zadovoljavaju zahtjeve moderne proizvodnje poluvodiča za visokom preciznošću i učinkovitošću. Zbog svojih jedinstvenih prednosti, lasersko rezanje postaje preferirano rješenje u tim područjima.
Iako se tehnologija laserskog rezanja još uvijek suočava s izazovima poput visokih troškova opreme i složenosti procesa, njezine jedinstvene prednosti u visokoj preciznosti i beskontaktnom oštećenju čine je važnim smjerom razvoja u proizvodnji poluvodiča. Kako laserska tehnologija i inteligentni upravljački sustavi nastavljaju napredovati, očekuje se da će lasersko rezanje dodatno poboljšati učinkovitost i kvalitetu rezanja pločica, potičući kontinuirani razvoj poluvodičke industrije.
2.3 Tehnologija rezanja plazmom
Tehnologija rezanja plazmom, kao nova metoda rezanja pločica, posljednjih je godina privukla značajnu pozornost. Ova tehnologija koristi visokoenergetske plazma zrake za precizno rezanje pločica kontroliranjem energije, brzine i putanje rezanja plazma zrake, postižući optimalne rezultate rezanja.
Princip rada i prednosti
Proces rezanja plazmom oslanja se na visokotemperaturnu, visokoenergetsku plazma zraku koju generira oprema. Ova zraka može zagrijati materijal pločice do točke taljenja ili isparavanja u vrlo kratkom vremenu, što omogućuje brzo rezanje. U usporedbi s tradicionalnim mehaničkim ili laserskim rezanjem, rezanje plazmom je brže i stvara manju zonu utjecaja topline, učinkovito smanjujući pojavu pukotina i oštećenja tijekom rezanja.
U praktičnim primjenama, tehnologija rezanja plazmom posebno je vješta u rukovanju pločicama složenih oblika. Njezina visokoenergetska, podesiva plazma zraka može lako rezati pločice nepravilnog oblika s visokom preciznošću. Stoga, u proizvodnji mikroelektronike, posebno u prilagođenoj i maloserijskoj proizvodnji vrhunskih čipova, ova tehnologija pokazuje veliki potencijal za široku upotrebu.
Izazovi i ograničenja
Unatoč mnogim prednostima tehnologije plazma rezanja, ona se suočava i s nekim izazovima.
• Složeni procesProces rezanja plazmom je složen i zahtijeva visokopreciznu opremu i iskusne operatere kako bi se osiguralotočnost i stabilnost pri rezanju.
• Kontrola okoliša i sigurnostVisokotemperaturna i visokoenergetska priroda plazma snopa zahtijeva stroge mjere kontrole okoliša i sigurnosti, što povećava složenost i troškove implementacije.
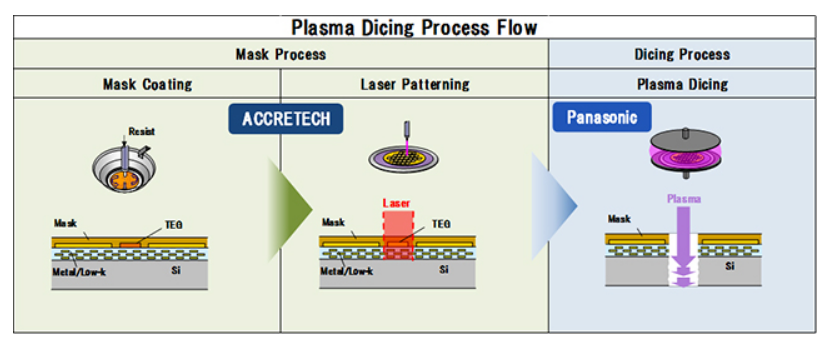
Budući pravci razvoja
Očekuje se da će se tehnološkim napretkom postupno prevladati izazovi povezani s rezanjem plazmom. Razvojem pametnije i stabilnije opreme za rezanje može se smanjiti ovisnost o ručnim operacijama, čime se poboljšava učinkovitost proizvodnje. Istovremeno, optimizacija parametara procesa i okruženja rezanja pomoći će u smanjenju sigurnosnih rizika i operativnih troškova.
U poluvodičkoj industriji, inovacije u tehnologiji rezanja i narezivanja pločica ključne su za poticanje razvoja industrije. Tehnologija rezanja plazmom, sa svojom visokom preciznošću, učinkovitošću i sposobnošću rukovanja složenim oblicima pločica, pojavila se kao značajan novi igrač u ovom području. Iako neki izazovi ostaju, ti će se problemi postupno rješavati kontinuiranim tehnološkim inovacijama, donoseći više mogućnosti i prilika proizvodnji poluvodiča.
Mogućnosti primjene tehnologije rezanja plazmom su ogromne i očekuje se da će u budućnosti igrati važniju ulogu u proizvodnji poluvodiča. Kontinuiranim tehnološkim inovacijama i optimizacijom, rezanje plazmom ne samo da će riješiti postojeće izazove, već će postati i snažan pokretač rasta industrije poluvodiča.
2.4 Kvaliteta rezanja i utjecajni faktori
Kvaliteta rezanja pločica ključna je za naknadno pakiranje čipa, testiranje te ukupne performanse i pouzdanost konačnog proizvoda. Uobičajeni problemi koji se javljaju tijekom rezanja uključuju pukotine, krhotine i odstupanja pri rezanju. Na te probleme utječe nekoliko čimbenika koji djeluju zajedno.
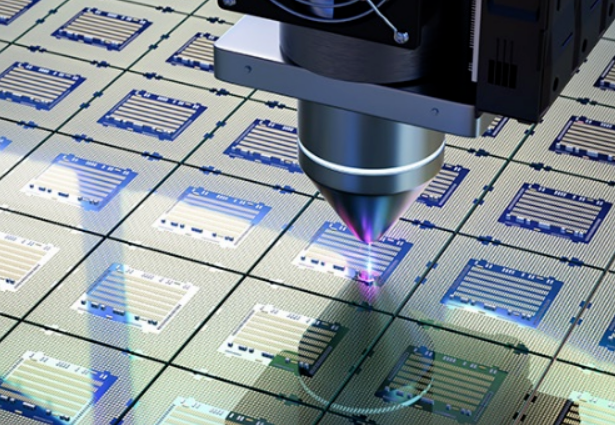
Kategorija | Sadržaj | Utjecaj |
Parametri procesa | Brzina rezanja, brzina pomaka i dubina rezanja izravno utječu na stabilnost i preciznost procesa rezanja. Nepravilne postavke mogu dovesti do koncentracije naprezanja i prekomjerne zone utjecaja topline, što rezultira pukotinama i ljuštenjem. Odgovarajuće podešavanje parametara na temelju materijala pločice, debljine i zahtjeva rezanja ključno je za postizanje željenih rezultata rezanja. | Pravi parametri procesa osiguravaju precizno rezanje i smanjuju rizik od nedostataka poput pukotina i odlomaka. |
Oprema i materijalni faktori | -Kvaliteta oštriceMaterijal, tvrdoća i otpornost na habanje oštrice utječu na glatkoću procesa rezanja i ravnost rezane površine. Oštrice loše kvalitete povećavaju trenje i toplinsko naprezanje, što potencijalno dovodi do pukotina ili ljuštenja. Odabir pravog materijala oštrice ključan je. -Performanse rashladne tekućineRashladna sredstva pomažu u smanjenju temperature rezanja, minimiziranju trenja i uklanjanju ostataka. Neučinkovita rashladna sredstva mogu dovesti do visokih temperatura i nakupljanja ostataka, što utječe na kvalitetu i učinkovitost rezanja. Odabir učinkovitih i ekološki prihvatljivih rashladnih sredstava je ključan. | Kvaliteta oštrice utječe na preciznost i glatkoću reza. Neučinkovito rashladno sredstvo može rezultirati lošom kvalitetom rezanja i učinkovitošću, što naglašava potrebu za optimalnom upotrebom rashladnog sredstva. |
Kontrola procesa i inspekcija kvalitete | -Kontrola procesaPraćenje i podešavanje ključnih parametara rezanja u stvarnom vremenu kako bi se osigurala stabilnost i dosljednost u procesu rezanja. -Inspekcija kvaliteteProvjere izgleda nakon rezanja, dimenzijska mjerenja i ispitivanja električnih performansi pomažu u brzom prepoznavanju i rješavanju problema s kvalitetom, poboljšavajući točnost i dosljednost rezanja. | Pravilna kontrola procesa i inspekcija kvalitete pomažu u osiguravanju dosljednih, visokokvalitetnih rezultata rezanja i ranom otkrivanju potencijalnih problema. |

Poboljšanje kvalitete rezanja
Poboljšanje kvalitete rezanja zahtijeva sveobuhvatan pristup koji uzima u obzir procesne parametre, odabir opreme i materijala, kontrolu procesa i inspekciju. Kontinuiranim usavršavanjem tehnologija rezanja i optimizacijom procesnih metoda, preciznost i stabilnost rezanja pločica mogu se dodatno poboljšati, pružajući pouzdaniju tehničku podršku industriji proizvodnje poluvodiča.
#03 Rukovanje i ispitivanje nakon rezanja
3.1 Čišćenje i sušenje
Koraci čišćenja i sušenja nakon rezanja pločice ključni su za osiguranje kvalitete čipa i nesmetan tijek sljedećih procesa. Tijekom ove faze bitno je temeljito ukloniti ostatke silicija, ostatke rashladne tekućine i druge nečistoće nastale tijekom rezanja. Jednako je važno osigurati da se čipovi ne oštete tijekom procesa čišćenja, a nakon sušenja osigurati da na površini čipa ne ostane vlage kako bi se spriječili problemi poput korozije ili elektrostatičkog pražnjenja.
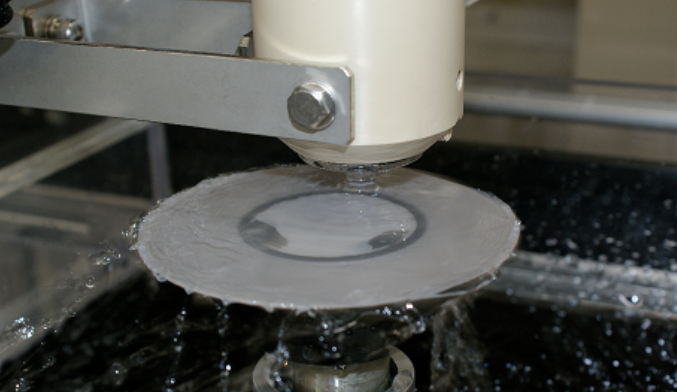
Rukovanje nakon rezanja: Proces čišćenja i sušenja
Korak procesa | Sadržaj | Utjecaj |
Proces čišćenja | -MetodaZa čišćenje koristite specijalizirana sredstva za čišćenje i čistu vodu, u kombinaciji s ultrazvučnim ili mehaničkim tehnikama četkanja. | Osigurava temeljito uklanjanje nečistoća i sprječava oštećenje strugotina tijekom čišćenja. |
-Odabir sredstva za čišćenjeOdaberite na temelju materijala pločice i vrste onečišćenja kako biste osigurali učinkovito čišćenje bez oštećenja čipa. | Pravilan odabir sredstva ključan je za učinkovito čišćenje i zaštitu od strugotina. | |
-Kontrola parametaraStrogo kontrolirajte temperaturu, vrijeme i koncentraciju otopine za čišćenje kako biste spriječili probleme s kvalitetom uzrokovane nepravilnim čišćenjem. | Kontrole pomažu u izbjegavanju oštećenja pločice ili ostavljanja nečistoća, osiguravajući dosljednu kvalitetu. | |
Proces sušenja | -Tradicionalne metodePrirodno sušenje zrakom i sušenje vrućim zrakom, koji imaju nisku učinkovitost i mogu dovesti do nakupljanja statičkog elektriciteta. | Može rezultirati sporijim vremenom sušenja i potencijalnim statičkim problemima. |
-Moderne tehnologijeKoristite napredne tehnologije poput vakuumskog sušenja i infracrvenog sušenja kako biste osigurali brzo sušenje čipsa i izbjegli štetne učinke. | Brži i učinkovitiji proces sušenja, smanjujući rizik od statičkog pražnjenja ili problema povezanih s vlagom. | |
Odabir i održavanje opreme | -Odabir opremeVisokoučinkoviti strojevi za čišćenje i sušenje poboljšavaju učinkovitost obrade i fino kontroliraju potencijalne probleme tijekom rukovanja. | Visokokvalitetni strojevi osiguravaju bolju obradu i smanjuju vjerojatnost pogrešaka tijekom čišćenja i sušenja. |
-Održavanje opremeRedoviti pregled i održavanje opreme osiguravaju optimalno radno stanje, jamčeći kvalitetu sječke. | Pravilno održavanje sprječava kvarove opreme, osiguravajući pouzdanu i visokokvalitetnu obradu. |
Čišćenje i sušenje nakon rezanja
Koraci čišćenja i sušenja nakon rezanja pločice složeni su i osjetljivi procesi koji zahtijevaju pažljivo razmatranje više čimbenika kako bi se osigurao konačni ishod obrade. Korištenjem znanstvenih metoda i strogih postupaka moguće je osigurati da svaki čip ulazi u sljedeće faze pakiranja i testiranja u optimalnom stanju.
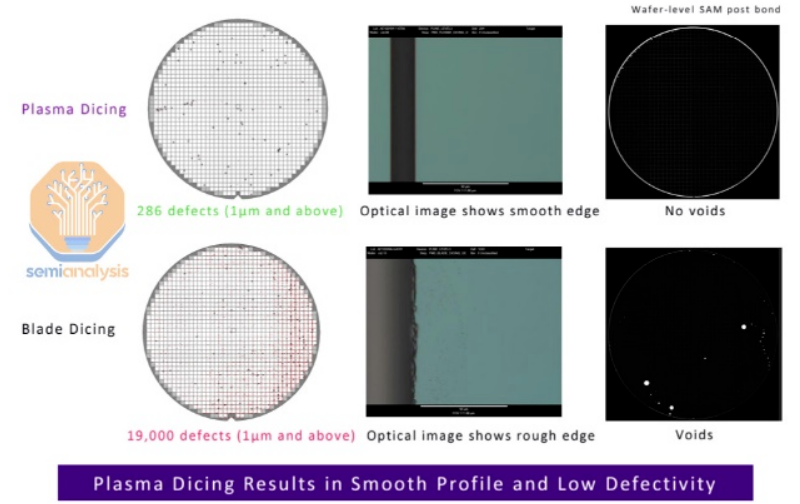
Inspekcija i ispitivanje nakon rezanja
Korak | Sadržaj | Utjecaj |
Korak inspekcije | 1.Vizualni pregledKoristite vizualnu ili automatiziranu opremu za pregled kako biste provjerili vidljive nedostatke poput pukotina, oštećenja ili onečišćenja na površini strugotine. Brzo identificirajte fizički oštećene strugotine kako biste izbjegli otpad. | Pomaže u ranom prepoznavanju i uklanjanju neispravnih strugotina u procesu, smanjujući gubitak materijala. |
2.Mjerenje veličineKoristite precizne mjerne uređaje za točno mjerenje dimenzija čipa, osiguravajući da veličina reza zadovoljava specifikacije dizajna i sprječavajući probleme s performansama ili poteškoće s pakiranjem. | Osigurava da su čipovi unutar potrebnih ograničenja veličine, sprječavajući smanjenje performansi ili probleme sa sastavljanjem. | |
3.Ispitivanje električnih performansiProcijenite ključne električne parametre poput otpora, kapaciteta i induktiviteta kako biste identificirali neusklađene čipove i osigurali da samo čipovi s kvalificiranim performansama prijeđu u sljedeću fazu. | Osigurava da se u procesu koriste samo funkcionalni i testirani čipovi, smanjujući rizik od kvara u kasnijim fazama. | |
Korak testiranja | 1.Funkcionalno testiranjeProvjeriti radi li osnovna funkcionalnost čipa kako je predviđeno, identificirati i ukloniti čipove s funkcionalnim abnormalnostima. | Osigurava da čipovi zadovoljavaju osnovne operativne zahtjeve prije nego što prijeđu na kasnije faze. |
2.Testiranje pouzdanostiProcijenite stabilnost performansi čipa pri duljoj upotrebi ili u teškim uvjetima, što obično uključuje starenje na visokim temperaturama, testiranje na niskim temperaturama i testiranje vlažnosti kako bi se simulirali ekstremni uvjeti u stvarnim uvjetima. | Osigurava pouzdan rad čipova u različitim uvjetima okoline, poboljšavajući dugovječnost i stabilnost proizvoda. | |
3.Testiranje kompatibilnostiProvjerite radi li čip ispravno s drugim komponentama ili sustavima, osiguravajući da nema grešaka ili smanjenja performansi zbog nekompatibilnosti. | Osigurava nesmetan rad u stvarnim aplikacijama sprječavanjem problema s kompatibilnošću. |
3.3 Pakiranje i skladištenje
Nakon rezanja pločice, čipovi su ključni proizvod procesa proizvodnje poluvodiča, a faze njihovog pakiranja i skladištenja jednako su važne. Pravilne mjere pakiranja i skladištenja ključne su ne samo za osiguranje sigurnosti i stabilnosti čipova tijekom transporta i skladištenja, već i za pružanje snažne podrške za naknadne faze proizvodnje, testiranja i pakiranja.
Sažetak faza inspekcije i ispitivanja:
Koraci inspekcije i testiranja čipova nakon rezanja pločice obuhvaćaju niz aspekata, uključujući vizualni pregled, mjerenje veličine, ispitivanje električnih performansi, funkcionalno ispitivanje, ispitivanje pouzdanosti i ispitivanje kompatibilnosti. Ovi koraci su međusobno povezani i komplementarni, tvoreći čvrstu barijeru za osiguranje kvalitete i pouzdanosti proizvoda. Strogim postupcima inspekcije i testiranja, potencijalni problemi mogu se identificirati i brzo riješiti, osiguravajući da konačni proizvod zadovoljava zahtjeve i očekivanja kupaca.
Aspekt | Sadržaj |
Mjere pakiranja | 1.AntistatičkoMaterijali za pakiranje trebaju imati izvrsna antistatička svojstva kako bi se spriječilo da statički elektricitet ošteti uređaje ili utječe na njihove performanse. |
2.Otporan na vlaguMaterijali za pakiranje trebaju imati dobru otpornost na vlagu kako bi se spriječila korozija i pogoršanje električnih performansi uzrokovano vlagom. | |
3.Otporan na udarceMaterijali za pakiranje trebaju osigurati učinkovitu apsorpciju udaraca kako bi zaštitili čips od vibracija i udaraca tijekom transporta. | |
Okruženje za pohranu | 1.Kontrola vlažnostiStrogo kontrolirajte vlažnost unutar odgovarajućeg raspona kako biste spriječili apsorpciju vlage i koroziju uzrokovanu prekomjernom vlagom ili statičkim problemima uzrokovanim niskom vlagom. |
2.ČistoćaOdržavajte čisto skladišno okruženje kako biste izbjegli kontaminaciju strugotine prašinom i nečistoćama. | |
3.Kontrola temperaturePostavite razuman temperaturni raspon i održavajte stabilnost temperature kako biste spriječili ubrzano starenje zbog pretjerane topline ili problema s kondenzacijom uzrokovanih niskim temperaturama. | |
Redovita inspekcija | Redovito pregledavajte i procjenjujte uskladištene čipove, koristeći vizualne preglede, mjerenja veličine i testove električnih performansi kako biste pravovremeno identificirali i riješili potencijalne probleme. Na temelju vremena i uvjeta skladištenja planirajte upotrebu čipova kako biste osigurali da se koriste u optimalnom stanju. |
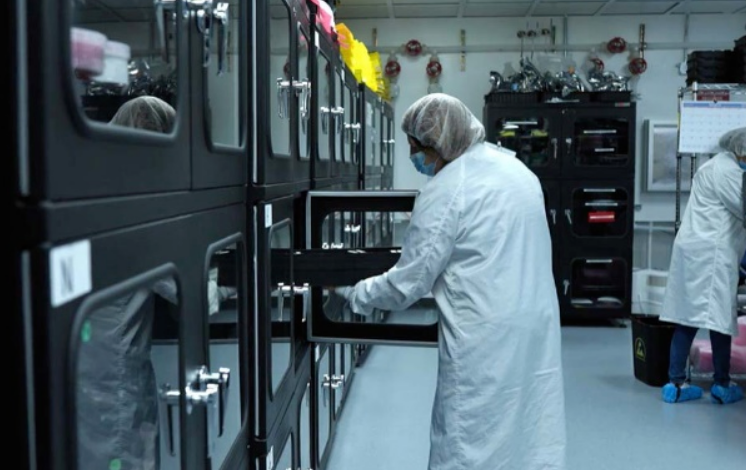
Problem mikropukotina i oštećenja tijekom procesa rezanja pločice značajan je izazov u proizvodnji poluvodiča. Naprezanje rezanja glavni je uzrok ovog fenomena, jer stvara sitne pukotine i oštećenja na površini pločice, što dovodi do povećanja troškova proizvodnje i smanjenja kvalitete proizvoda.
Kako bi se riješio ovaj izazov, ključno je minimizirati naprezanje rezanja i primijeniti optimizirane tehnike rezanja, alate i uvjete. Pažljivo praćenje čimbenika poput materijala oštrice, brzine rezanja, tlaka i metoda hlađenja može pomoći u smanjenju stvaranja mikropukotina i poboljšanju ukupnog prinosa procesa. Osim toga, tekuća istraživanja naprednijih tehnologija rezanja, poput laserskog rezanja, istražuju načine za daljnje ublažavanje ovih problema.
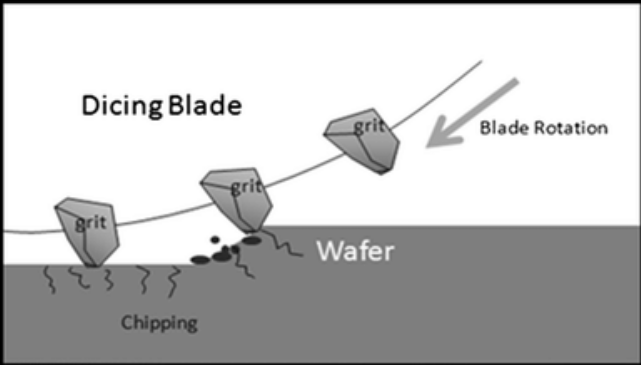
Kao krhki materijal, pločice su sklone unutarnjim strukturnim promjenama kada su izložene mehaničkom, toplinskom ili kemijskom naprezanju, što dovodi do stvaranja mikropukotina. Iako te pukotine možda nisu odmah uočljive, mogu se proširiti i uzrokovati ozbiljnija oštećenja kako proizvodni proces napreduje. Ovaj problem postaje posebno problematičan tijekom sljedećih faza pakiranja i testiranja, gdje temperaturne fluktuacije i dodatna mehanička naprezanja mogu uzrokovati da se te mikropukotine razviju u vidljive lomove, što potencijalno može dovesti do kvara čipa.
Kako bi se ublažio ovaj rizik, bitno je pažljivo kontrolirati proces rezanja optimizacijom parametara poput brzine rezanja, tlaka i temperature. Korištenje manje agresivnih metoda rezanja, poput laserskog rezanja, može smanjiti mehaničko naprezanje pločice i minimizirati stvaranje mikropukotina. Osim toga, primjena naprednih metoda inspekcije poput infracrvenog skeniranja ili rendgenskog snimanja tijekom procesa rezanja pločice može pomoći u otkrivanju ovih pukotina u ranoj fazi prije nego što uzrokuju daljnja oštećenja.
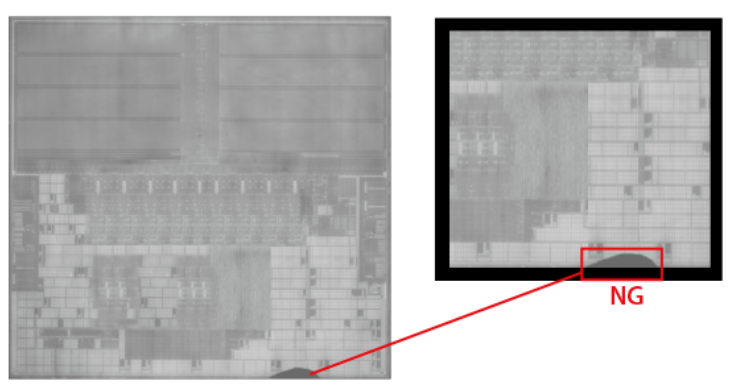
Oštećenje površine pločice značajan je problem u procesu rezanja, jer može imati izravan utjecaj na performanse i pouzdanost čipa. Takva oštećenja mogu biti uzrokovana nepravilnom upotrebom alata za rezanje, netočnim parametrima rezanja ili materijalnim nedostacima svojstvenim samoj pločici. Bez obzira na uzrok, ta oštećenja mogu dovesti do promjena u električnom otporu ili kapacitetu kruga, što utječe na ukupne performanse.
Za rješavanje ovih problema istražuju se dvije ključne strategije:
1. Optimizacija alata i parametara za rezanjeKorištenjem oštrijih oštrica, podešavanjem brzine rezanja i mijenjanjem dubine rezanja, koncentracija naprezanja tijekom procesa rezanja može se smanjiti, čime se smanjuje mogućnost oštećenja.
2. Istraživanje novih tehnologija rezanjaNapredne tehnike poput laserskog rezanja i rezanja plazmom nude poboljšanu preciznost, a istovremeno potencijalno smanjuju razinu oštećenja nanesenih pločici. Ove se tehnologije proučavaju kako bi se pronašli načini za postizanje visoke točnosti rezanja uz minimiziranje toplinskog i mehaničkog naprezanja na pločici.
Područje toplinskog utjecaja i njegov utjecaj na performanse
U termičkim procesima rezanja poput laserskog i plazma rezanja, visoke temperature neizbježno stvaraju zonu toplinskog udara na površini pločice. Ovo područje, gdje je temperaturni gradijent značajan, može promijeniti svojstva materijala, utječući na konačne performanse čipa.
Utjecaj termički pogođene zone (TAZ):
Promjene kristalne strukturePod utjecajem visokih temperatura, atomi unutar materijala pločice mogu se preurediti, uzrokujući izobličenja u kristalnoj strukturi. Ovo izobličenje slabi materijal, smanjujući njegovu mehaničku čvrstoću i stabilnost, što povećava rizik od kvara čipa tijekom upotrebe.
Promjene električnih svojstavaVisoke temperature mogu promijeniti koncentraciju i pokretljivost nositelja naboja u poluvodičkim materijalima, utječući na električnu vodljivost čipa i učinkovitost prijenosa struje. Ove promjene mogu dovesti do smanjenja performansi čipa, što ga potencijalno čini neprikladnim za njegovu namjenu.
Kako bi se ublažili ovi učinci, kontrola temperature tijekom rezanja, optimizacija parametara rezanja i istraživanje metoda poput mlazova za hlađenje ili naknadne obrade ključne su strategije za smanjenje opsega toplinskog utjecaja i održavanje integriteta materijala.
Sveukupno, i mikropukotine i zone toplinskog udara ključni su izazovi u tehnologiji rezanja pločica. Kontinuirana istraživanja, uz tehnološki napredak i mjere kontrole kvalitete, bit će potrebna za poboljšanje kvalitete poluvodičkih proizvoda i povećanje njihove tržišne konkurentnosti.
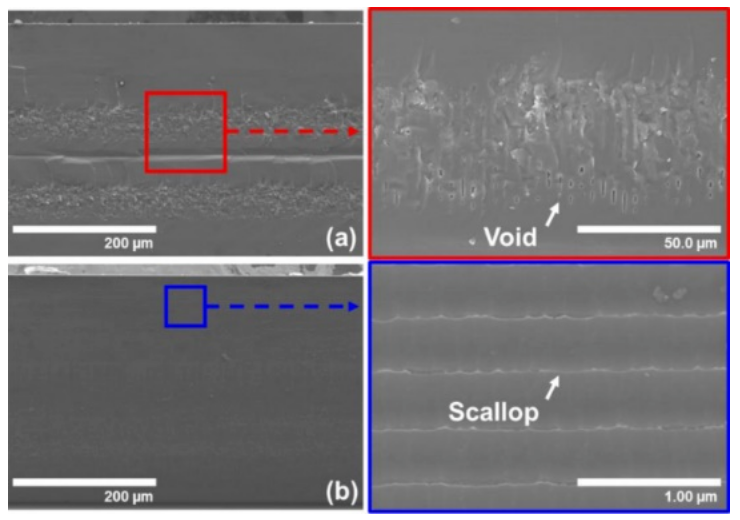
Mjere za kontrolu zone toplinskog utjecaja:
Optimizacija parametara procesa rezanjaSmanjenje brzine i snage rezanja može učinkovito smanjiti veličinu zone toplinskog udara (TAZ). To pomaže u kontroli količine topline koja se stvara tijekom procesa rezanja, što izravno utječe na svojstva materijala pločice.
Napredne tehnologije hlađenjaPrimjena tehnologija poput hlađenja tekućim dušikom i mikrofluidnog hlađenja može značajno ograničiti raspon zone toplinskog udara. Ove metode hlađenja pomažu u učinkovitijem odvođenju topline, čime se čuvaju materijalna svojstva pločice i minimiziraju toplinska oštećenja.
Odabir materijalaIstraživači istražuju nove materijale, poput ugljikovih nanocjevčica i grafena, koji posjeduju izvrsnu toplinsku vodljivost i mehaničku čvrstoću. Ovi materijali mogu smanjiti zonu toplinskog udara, a istovremeno poboljšati ukupne performanse čipova.
Ukratko, iako je zona toplinskog udara neizbježna posljedica tehnologija termičkog rezanja, može se učinkovito kontrolirati optimiziranim tehnikama obrade i odabirom materijala. Buduća istraživanja vjerojatno će se usredotočiti na fino podešavanje i automatizaciju procesa termičkog rezanja kako bi se postiglo učinkovitije i preciznije rezanje pločica.

Strategija ravnoteže:
Postizanje optimalne ravnoteže između prinosa pločica i učinkovitosti proizvodnje stalni je izazov u tehnologiji rezanja pločica. Proizvođači moraju uzeti u obzir više čimbenika, kao što su tržišna potražnja, troškovi proizvodnje i kvaliteta proizvoda, kako bi razvili racionalnu strategiju proizvodnje i parametre procesa. Istovremeno, uvođenje napredne opreme za rezanje, poboljšanje vještina operatera i poboljšanje kontrole kvalitete sirovina ključni su za održavanje ili čak poboljšanje prinosa uz povećanje učinkovitosti proizvodnje.
Budući izazovi i prilike:
S napretkom poluvodičke tehnologije, rezanje pločica suočava se s novim izazovima i prilikama. Kako se veličine čipova smanjuju, a integracija povećava, zahtjevi za preciznošću i kvalitetom rezanja značajno rastu. Istovremeno, nove tehnologije pružaju nove ideje za razvoj tehnika rezanja pločica. Proizvođači moraju pratiti dinamiku tržišta i tehnološke trendove, kontinuirano prilagođavajući i optimizirajući proizvodne strategije i parametre procesa kako bi zadovoljili promjene na tržištu i tehnološke zahtjeve.
Zaključno, integriranjem razmatranja tržišne potražnje, troškova proizvodnje i kvalitete proizvoda te uvođenjem napredne opreme i tehnologije, poboljšanjem vještina operatera i jačanjem kontrole sirovina, proizvođači mogu postići najbolju ravnotežu između prinosa pločice i učinkovitosti proizvodnje tijekom rezanja pločice, što dovodi do učinkovite i visokokvalitetne proizvodnje poluvodičkih proizvoda.
Budući izgledi:
S brzim tehnološkim napretkom, tehnologija poluvodiča napreduje neviđenom brzinom. Kao ključni korak u proizvodnji poluvodiča, tehnologija rezanja pločica spremna je za uzbudljive nove razvoje. Gledajući u budućnost, očekuje se da će tehnologija rezanja pločica postići značajna poboljšanja u preciznosti, učinkovitosti i troškovima, ubrizgavajući novu vitalnost u kontinuirani rast industrije poluvodiča.
Povećanje preciznosti:
U potrazi za većom preciznošću, tehnologija rezanja pločica kontinuirano će pomicati granice postojećih procesa. Dubinskim proučavanjem fizičkih i kemijskih mehanizama procesa rezanja i preciznom kontrolom parametara rezanja, postići će se finiji rezultati rezanja kako bi se zadovoljili sve složeniji zahtjevi dizajna sklopova. Osim toga, istraživanje novih materijala i metoda rezanja značajno će poboljšati prinos i kvalitetu.
Povećanje učinkovitosti:
Nova oprema za rezanje pločica usredotočit će se na pametan i automatizirani dizajn. Uvođenje naprednih upravljačkih sustava i algoritama omogućit će opremi automatsko podešavanje parametara rezanja kako bi se prilagodila različitim materijalima i zahtjevima dizajna, čime se značajno poboljšava učinkovitost proizvodnje. Inovacije poput tehnologije rezanja više pločica i sustava za brzu zamjenu oštrica igrat će ključnu ulogu u povećanju učinkovitosti.
Smanjenje troškova:
Smanjenje troškova ključni je smjer razvoja tehnologije rezanja pločica. Razvojem novih materijala i metoda rezanja očekuje se učinkovita kontrola troškova opreme i održavanja. Osim toga, optimizacija proizvodnih procesa i smanjenje stope otpada dodatno će smanjiti otpad tijekom proizvodnje, što će dovesti do smanjenja ukupnih troškova proizvodnje.
Pametna proizvodnja i IoT:
Integracija pametne proizvodnje i tehnologija Interneta stvari (IoT) donijet će transformativne promjene u tehnologiju rezanja pločica. Međusobnom povezanošću i dijeljenjem podataka između uređaja, svaki korak proizvodnog procesa može se pratiti i optimizirati u stvarnom vremenu. To ne samo da poboljšava učinkovitost proizvodnje i kvalitetu proizvoda, već i tvrtkama pruža točnije predviđanje tržišta i podršku u donošenju odluka.
U budućnosti će tehnologija rezanja pločica ostvariti izvanredan napredak u preciznosti, učinkovitosti i troškovima. Ovi će napredci potaknuti daljnji razvoj poluvodičke industrije i donijeti više tehnoloških inovacija i pogodnosti ljudskom društvu.
Vrijeme objave: 19. studenog 2024.